注塑外模具廠在注塑生產(chǎn)過程中常常遇到產(chǎn)品頂白的現(xiàn)象,很多注塑廠家遇上這種頂白現(xiàn)象時(shí),為了趕貨只好作臨時(shí)的辦法就是使用脫模劑。但使用脫模劑又會(huì)直接影響產(chǎn)品的外觀,甚用多了會(huì)破產(chǎn)品的塑料性質(zhì)從而降低產(chǎn)品的日后使用功效。而且使用脫模劑也增加了生產(chǎn)成本。所以,加工廠要產(chǎn)品頂白現(xiàn)象建議是從模具頂出結(jié)構(gòu)入手。
Injection mold factories often encounter the phenomenon of product top white in the injection production process. When many injection mold manufacturers encounter this phenomenon, they have to make a temporary solution in order to catch up with the goods is to use release agent. However, the use of release agent will directly affect the appearance of the product, and even more use will damage the plastic properties of the product, thus reducing the future use efficiency of the product. And the use of release agent also increases the production cost. Therefore, the suggestion for the processing plant to solve the product top white phenomenon is to start with the mold ejection structure.
廠家要徹底產(chǎn)品頂白現(xiàn)象,必須檢查在頂白的部位是否能加頂針,是否有骨位沒有省光省滑,如果有骨位還存在火花紋沒省干凈是易造成頂白的。再有一個(gè)原因是產(chǎn)品某部位出模斜度不夠,如果是這個(gè)原因就必須重新加工,保證有足夠的出模斜度才可以切斷頂白現(xiàn)象的,否則任你如何省光省滑或加頂針都無法徹底頂白的。
In order to completely solve the problem of product top whiteness, the manufacturer must check whether a thimble can be added at the top whiteness part, whether there is a bone position that does not save light and slip, and if there is a bone position that still has spark lines, it is easy to cause top whiteness. Another reason is that a certain part of the product has insufficient mold inclination. If this is the reason, it must be reprocessed to ensure that there is enough mold inclination before the top white phenomenon can be cut off. Otherwise, no matter how you save light and slip or add a thimble, the top white problem can not be completely solved.
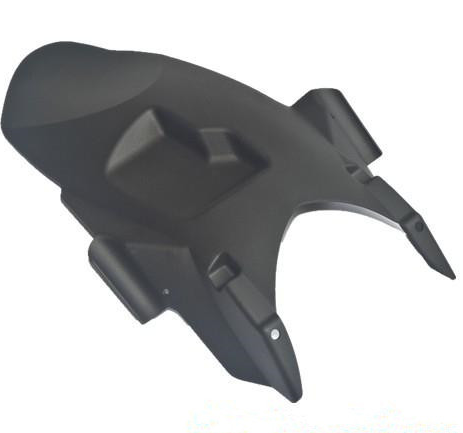
塑件出現(xiàn)頂白現(xiàn)象的原因主要是制品粘模力較大,而塑件上頂出部位致頂桿頂出位置產(chǎn)生白痕。
山東模具制造廠家給您分析下具體的原因和改善方法,如下:
The main reason for the top white phenomenon of plastic parts is that the product has a large mold adhesion force, and the top part of the plastic parts causes white marks on the top position of the ejector rod. The Shandong mold manufacturer will analyze the specific causes and improvement methods for you, as follows:
1,后模溫度太低或太高:調(diào)整合適的模溫。
1. The rear mold temperature is too low or too high: adjust the appropriate mold temperature.
2,頂出速度過快:減慢頂出速度。
2. Too fast ejection speed: slow down the ejection speed.
3,有脫模倒角:檢修模具(拋光)。
3. With demoulding chamfer: repair the mold (polishing).
4,成品頂出不平衡(斷頂針板彈簧):檢修模具(使頂出平衡)。
4. The ejection of finished products is unbalanced (the ejector pin plate spring is broken): repair the mold (make the ejection balanced).
5,頂針數(shù)量不夠或位置不當(dāng):增加頂針數(shù)量或改變頂針位置。
5. Insufficient number or improper position of ejector pins: increase the number of ejector pins or change the position of ejector pins.
6,脫模時(shí)模具產(chǎn)生真空現(xiàn)象:清理頂針孔內(nèi)污漬,改善進(jìn)氣效果。
6. Vacuum occurs in the mold during demoulding: clean the dirt in the ejector pin hole to improve the air inlet effect.
7,成品骨位、柱位粗糙(倒扣):拋光各骨位及柱位。
7. The finished bone position and column position are rough (inverted): polish each bone position and column position.
8,注射壓力或保壓壓力過大:適當(dāng)降低其壓力。
8. Excessive injection pressure or holding pressure: reduce the pressure appropriately.
9,成品后模脫模斜度過?。涸龃蠛竽C撃P倍?。
9. The demoulding slope of the finished product rear mold is too small: increase the demoulding slope of the rear mold.
10,側(cè)滑塊動(dòng)作時(shí)間或位置不當(dāng):檢修模具(使抽芯動(dòng)作正常)。
10. Improper action time or position of the side slider: repair the mold (make the core pulling action normal).
11,頂針面積太小或頂出速度過快:增大頂針面積或減慢頂出速度。
11. The ejector pin area is too small or the ejection speed is too fast: increase the ejector pin area or slow down the ejection speed.
12,末段的注射速度過快(毛刺):減慢較后一段注射速度。
12. The injection speed of the last section is too fast (Burr): it slows down the injection speed of the later section.
以上便是注塑加工產(chǎn)品出現(xiàn)頂白的原因和方法,那么如果您想了解更多信息,就來關(guān)注我們網(wǎng)站
www.195ty.com吧,讓您滿載而歸!
These are the reasons and solutions for the top white of injection molding products. If you want to learn more, please follow our website www.sdlqmj COM, let you return with a full load!